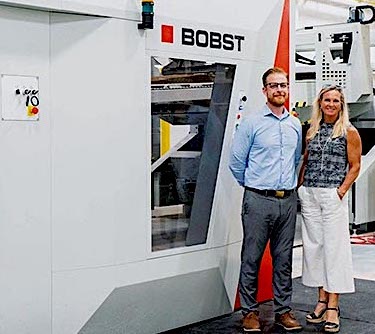
Royal Containers (Brampton and St. Thomas, Ontario), one of Canada’s largest producers of corrugated packaging made from 100% recycled papers, has successfully installed a Bobst Masterdro Flexographic Rotary Die Cutter with inside-outside print capabilities – the first of its kind in North America. Royal Containers generates about $100 million in annual sales from its two production facilities, and has over 300 employees. The new die cutter sits alongside a Bobst DRO 1628 NT Rotary Die Cutter and a new Bobst Expertfold Folder-Gluer which was installed in July of this year.
Having acquired Morphy Containers in London, Ontario in 2009, and a decade later C&B Display Packaging in Brampton, Ontario, the company was faced with the situation of having two business units operating in close proximity. “We needed to invest in some new equipment for the old Morphy facility, and we also had eyes on new machinery for C&B as well,” explained President Kim Nelson. “So, we took the rather bullish approach of buying a new, bigger facility, and then combining both operations into one. Of course, the culture of a packaging business and a display business don’t necessarily blend easily – one being driven by volume, the other by graphics and design – but we believed we could marry the operations together. And then of course, COVID-19 hit, literally weeks before we signed the documents on the acquisition of C&B – not ideal timing, but we are never afraid of a challenge.”
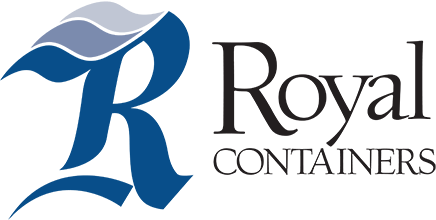
The company subsequently found a 155,000-sq.-ft. facility in nearby St. Thomas, Ontario that was a perfect fit. “Although it was a great find, we knew we had to do a lot of groundwork before we could move equipment,” Nelson added. “Although St. Thomas is a relatively small town, it was a great area for us, as there had been significant investment by some other large businesses, including Amazon. It was a perfect fit. Without hesitation, I knew we had to have the Bobst die cutter. We have a wide array of print capabilities at Royal Containers and adding inside-outside print in a single pass was something we wanted. We were already producing this kind of e-commerce pack and had to do it in multiple passes, which was time consuming. I knew our sales team would be able to fill this new machine, so we set about working with Bobst to install what was to be the first machine of its kind in North America.”

Switzerland-based OEM Bobst launched its Masterdro Flexographic Rotary Die Cutter as part of its Masterline Dro Series – a full-line solution from pre-feeder to palletizer – in 2021. Incorporating the latest Bobst technology including 10 patents, the line equips converters with a versatile, fully automated, connected and highly ergonomic solution. The machine can output more than 40 million sqm (430 million sq. ft.) per year, combining high-volume production on simple boxes and added-value packaging, with qualitative printing and die cutting. The high quality provided by the Masterdro is consistent for each item, and boxes traditionally benefit from a 15% improvement in the box compression test (BCT), which represents huge potential savings on paper use.
Its two quality control systems enable “perfect” printing register consistency during setup or during production. ‘Start & Go’ technology provides fully automatic set-up of multi-colour jobs with automatic compensation of cliché irregularities with only 11 sheets, while ‘Lead & Print’ guarantees print-to-print and print-to-cut consistency with proactive compensation of board irregularities during production. The machine also has an efficient dust-collection system on both sides of the sheet to ensure maximum printing quality, and a die-cutting efficiency that ejects over 99.9% of die-cut waste.
Thank you for your sharing. I am worried that I lack creative ideas. It is your article that makes me full of hope. Thank you. But, I have a question, can you help me? [Link deleted]